Using this technology not only to make gasoline but two keep smoke and other dream house gases from escaping into the atmosphere, by using a water filter filtration system. Of course you can use multiple Chambers so not even one particle of carbon emissions or other unwanted things you don't want in your breathing it is filtered by the water oh, look at the below video to see how that will work.
it may not be totally green but it is renewable energy, you're going to use your fallen leaves and grass clippings to make your own pellets to burn in your stove. Using natural resources without destroying nature.
we suggest that you run the smokestack down and through water, not only does it act as a natural filter but it also catches natural oils that can be reused in your stove, this makes this stove almost green
List:
Pine cones
Helicopters
Pine needles
Leaves
Even acorns
There are many other annoying things that we throw away to be hauled off as trash that we could use to make a renewable biofuel
THERMOELECTRIC GENERATOR PRODUCTS FOR SALE
WOOD STOVE TEGS & MORE!
TEGMART is your online store for TEG Power Wood Stove Thermoelectric Generators, TEG Modules, Energy Harvesting Circuits, Plug & Play TEG Systems and more! We have a strong knowledge base and videos demonstrating our Propane Camping Thermoelectric Generators & Wood Stove TEGs to supply power to devices in your homes, camps, tents and ice fishing shanties. Also, you’ll find heatsinks including water cooling blocks and Torque Screwdrivers to properly clamp TEG Generator Modules.
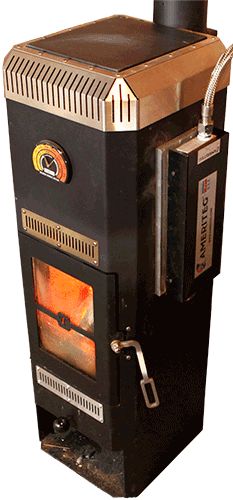
WHAT IS TEG POWER AND WHAT ARE THERMOELECTRIC GENERATORS?
A Thermoelectric Generator is a solid state device that converts temperature differences into electrical energy or TEG Power, using a phenomenon called the "Seebeck effect" . Their typical efficiencies are around 5% - 8%. When heat is applied to the hot side of a Thermoelectric Generator, electricity is produced. Almost any heat source (i.e. Wood Stove) can be used to harness TEG Power, such as solar heat, geothermal heat, even body heat. In addition, the efficiency of any device or machine that generates heat as a by-product can be drastically improved by recovering the energy lost as heat.
PATENT PENDING MAGNETIC THERMOELECTRIC GENERATORS TO BE RELEASED SOON...
Soon we will be releasing a patent pending magnetic mounting & uncoupling Thermoelectric Generator. They will be the only Thermoelectric Generators made in the USA with US made Thermoelectric Modules featuring the ability to couple & uncouple from High Temperature Heat Sources. The patent pending power management technology will feature MPPT tracking Thermoelectric Generators, which will be able to charge various battery
TEGMART NEWS
11 Homemade Glue Recipes
You can make your own homemade glue – even specialty crafting glues. Why would you want to do that? Well, it’s true that store-bought glue is mostly cheap and effective, though some specialty glues are expensive and hard to find. With these homemade glue recipes, you might in some cases be able to make a better glue for your purposes, especially if you’re doing an arts or crafts projectwith particular needs.
Basically, making your own glue is a form of crafting. You do it mainly because it’s fun, interesting and educational (many of these glue recipes are safe for kids to help with).
You may want to get some reusable glue bottles like these I got from Amazon. They have a good size opening for refilling, and I haven’t had any trouble with leaking. And if you need some craft ideas to do with kids, check out Martha Stewart’s Favorite Crafts for Kids: 175 Projects for Kids of All Ages. It’s written for adults who are helping little kids (as young as 2) learn to craft. My glue recipes #2-4 are great for craft items like the super-cute Cotton Ball Sheep and the Paper Bag Puppets.
US Made Thermoelectric Generators
Tegpro currently makes AmeriTEG, the only Thermoelectric Generator for Wood and Gas Stoves that is made in the USA with US Made thermoelectric modules. The AmeriTEG Water and Air Cooled models employ their patent pending magnetic coupling technology with their patent pending Energy Management technology that features power prioritization, maxium power point tracking (MPPT) and wireless telemetry (including stove performanace) via Bluetooth/Wifi. Tegpro is also produces the Stove Lite, Thermoelectric Generator Lantern which will also be made in their US based factory in Randolph, VT. The Stove Lite is available for purchase at Tegmart.
Featured above are American Made Products by Tegpro. Note the Water Cooled and Air Cooled Magnetic Thermoelectric Generators!
What are Thermoelectric Generator Modules?Thermoelectric generator modules are solid-state integrated circuits that employ the Seebeck effect. It is the Seebeck effect that is responsible for electrical power generation and thus the foundation of TEG Power Modules. Thermoelectric Generator Modules are the heart of any Thermoelectric Generator. The thermoelectric generator module is located between the heat receiving surface and heat exiting surface of a thermoelectric generator. The heat from the heat receiving surface passes through the Thermoelectric Generator Module. While most of the heat passes through to the heat exiting surface a portion of it is converted to electrical current. Companies like Tegpro manufacture low & high temperature Thermoelectric Genrator modules for a myriad of applications.You can learn more about Thermoelectric Generators by visiting the links on our Tools page.
Tegpro Thermoelectric Generator Modules available at Tegmart
How are Thermoelectric Generator Modules made?Construction of a Teg Power Module consists of pairs of p-type and n-type semiconductor materials with a high thermoelectric coefficient. Although many alloys can be used, bismuth telluride is the most common material used today. This material is sliced into small blocks, one forms the p-type conductor and the other the n-type conductor. Each pair forms a thermoelectric couple (TEC). These thermocouples are most often connected electrically forming an array of multiple thermocouples (thermopile). Unlike solder used in the construction of TEC's, thermoelectric generator modules often require solders that reflow well in excess of 400 C. |
Most thermoelectric generator module manufacturing companies use many thermoelectric couples that are sandwiched between two pieces of non-electrically conductive materials. It is also necessary for this material to be thermally conductive to ensure a good heat transfer, usually two thin ceramic wafers are used, to form what is called a thermoelectric module.
Each module can contain dozens of pairs of thermoelectric couples called thermoelectric generator modules, TEC modules and sometimes Peltier or, Seebeck modules, which simply denotes whether they are being used to generate electricity (Seebeck) or produce heat or cold (Peltier). Functionally there is no difference between the two. They both are capable of producing heat and cold or generating electricity, depending on whether heat is applied or an electrical current.
There are however differences in performance between various modules depending on what they were manufactured for. For example, if a module is being manufactured for use in a 12 volt dc automotive cooler the thermoelectric couples will be of a thicker gage and so will the wire connecting the modules to the 12 volt dc power source. In most cases the module itself is quite large. This is simply because the module will be conducting a heavy load of current and will need to be able to handle the load. Although these type modules can be used to produce electricity they are not well suited for the task because they have a high internal resistance (lowering output) and lower temperature solder that may melt if used for Seebeck purposes. Meaning the electrical connection may fail when the higher heat needed to produce significant amounts of electricity is applied to the module.
If a thermoelectric module is being manufactured for use in a thermoelectric generator it has its own unique requirements. First they need to have lowest internal resistance and high temperature solder comprising of sivler for example, to connect the wires. Also PTFE or Fiberglass coated wire must be employed to handle the high temperatures. Silicoon fiberglass sleeves can be slipped over the wires can provide more protection from the high temperatures.
What is a TEG Power Generator?
TEG is an acronym for ‘thermoelectric generator’. A TEG is a device utilizing one or more thermoelectric models as the primary component/s, followed by a cooling system that can be either passive or active. An open air heat sink, fan cooled heat sink, or hydronics cooling system are examples of ways to cool Thermoelectric Generators. These components are then fabricated into an assembly to function as one unit called a TEG. Often when an active cooling system is required, electronics and firmware are needed to prioritize power to ensure the system is adequately cooled. Products like this one offered at Tegmart are designed to ensure that the active cooling system always is given priority before any net gain of power can be utilized. This also allows some devices to start up on their own power rather than rely on a battery system to start, especially if the battery system is completely depleted.
When heat is applied to the hot side of a TEG, electricity is produced. Almost any heat source can be used to generate electricity, such as solar heat, geothermal heat, even body heat! In addition the efficiency of any device or machine that generates heat as a by-product can be drastically improved by recovering the energy lost as heat. Many companies are now realizing the potential of Thermoelectric Generators in heating systems, to lessen the demand on the grid as well as self-power the device in the event of power outages.
Can you really generate that much electricity from waste heat?You may be surprised just how much you can! Even though a Wood Stove is not considered a waste heat source, below is an example of how much power you can generate. Below is a 15 Watt Devil Watt Generator built with Tegpro thermoelectric modules. The output from this simple thermoelectric generator (TEG) is up to 15 watts and the light is a 10 watt EverLed LVL2 flush mount fixture. Tegpro has designed Thermoelectric Generators for Wood Stoves that have exceeded 200 Watts in Thermoelectric Power Generation! |
Almost any heat source can be used to generate electricity, candles, home heating systems, space heaters, water cooled boat motors, gas/propane water heaters, industrial waste heat from foundries, gas lights and many more!
Thermoelectric Generator Advantages . . . | NOTE: One 800 watt solar panel produces 2.4 kWh of electricity per day in Northern Vermont. A Thermoelectric Generator System that averages 100 watts an hour implemented on a heating system, such as a wood stove, can also produces 2.4kWh of electricity per day, (provided you have 24 hr continuous heat source). When you compare the costs of solar and thermoelectric generators living in the cold northern climate (based on the actual amount of electricity they actually produce per day) you'll find that TEG Power Thermoelectric Generators cost far less per kWh than solar. The Photovoltaic equivalent of 100 watts of TEG power operating on a wood stove is 660 watts of solar panels or 2.4 kWh per day. This means that averaging 125 watts of thermoelectric power in a Vermont house can produce the same amount of electricity in a day as 1000 watts of solar PV panels. If comparing costs, the price range for 1000 watts of solar would be as much as $3,000 depending on the particular brand. Whereas the cost of 125 watts of thermoelectric power can be as low as $1,200. Unlike solar, TEGs aren't dependent on the sun to produce power. If you have a continuous heat source, like a wood or pellets, TEGs can produce power 24 hours a day. Unlike fossil fuel generators, TEGs have few moving parts, other than cooling fans or water cooling pumps, and can be rated to last for more than 100,000 hours of continuous operation. |
Thermoelectric Home Power
Thermoelectric generators can provide supplemental electricity for home owners who use wood/biofuel furnaces or stoves. The video below reflects just one of the possible thermoelectric home power stations that could be setup using TEG Power modules. It should be noted that just 250 watts of thermoelectric power added to a wood/propane stove like the one below can produce almost 6 kWh of electricity per day, which is enough to reduce the average Vermont household electric bill by more than one third. The majority of new wood burning stoves/furnaces now use gasification technology which produces clean burning hydrogen gas, making them extremely efficient and clean burning. EPA approved wood stoves/furnaces are eligible for a federal tax credits. Here is an example of a new TEG Power Generator System for converting heat to electricty from a Wood Stove.
Note: The Video on the Left is showing an Englander NC-30 Wood Stove with 2 Devil Watt 50 Watt Water Cooled TEGs with Tegpro's patent pending TEG Power Energy Management System. Check out the complete system at Tegmart. |
A Need for Thermoelectric Generator Power
Electricity is a necessity. If you've ever had to suffer through an extended power outage, you'd know what it is like to loose all the food in your refrigerator. If you live in a cold climate your house was cold because you have no heat, as the majority of heating systems require powetr to run. Every millions of folks have been in this position when a winter storm knocked out power over large areas.
Solar panels are a great renewable energy source, but they only produce power in the daytime. Their daily output is significantly reduced during the shorter days in the winter months. Using TEG Power Generators in cold climates, in conjunction with solar, can provide all off your home’s energy needs.
TEG Power Modules vs. TEG Power Generators
It's not correct to refer to a TEG Power module as a “TEG Power Generator”. The thermoelectric generator modules are just one electrical component. They are the equivalent of an LED, in a lighting fixture. To generate Thermoelectric Power, you must design/build a TEG Power Generator, which involves heat receiving/heat exiting plates, thermally conductive materials such as graphite, heat sinks/fan sinks to transform a thermoelectric module into a thermoelectric generator. Some systems require active cooling with a micro-controlled electronics package. Tegpro specializes in active cooling control systems.
A mill is a device that breaks solid materials into smaller pieces by grinding, crushing, or cutting. Such comminution is an important unit operation in many processes. There are many different types of mills and many types of materials processed in them. Historically mills were powered by hand (e.g., via a hand crank), working animal (e.g., horse mill), wind (windmill) or water (watermill). Today they are usually powered by electricity.
The grinding of solid materials occurs through mechanical forces that break up the structure by overcoming the interior bonding forces. After the grinding the state of the solid is changed: the grain size, the grain size disposition and the grain shape.
Milling also refers to the process of breaking down, separating, sizing, or classifying aggregate material. For instance rock crushing or grinding to produce uniform aggregate size for construction purposes, or separation of rock, soil or aggregate material for the purposes of structural fill or land reclamation activities. Aggregate milling processes are also used to remove or separate contamination or moisture from aggregate or soil and to produce "dry fills" prior to transport or structural filling.
Grinding may serve the following purposes in engineering:
- increase of the surface area of a solid
- manufacturing of a solid with a desired grain size
- pulping of resources
Grinding laws
In spite of a great number of studies in the field of fracture schemes there is no formula known which connects the technical grinding work with grinding results. To calculate the needed grinding work against the grain size changing three semi-empirical models are used. These can be related to the Hukki relationship between particle size and the energy required to break the particles. In stirred mills, the Hukki relationship does not apply and instead, experimentation has to be performed to determine any relationship.[1]
- Kick for d > 50 mm
- Bond[2] for 50 mm > d > 0.05 mm
- Von Rittinger for d < 0.05 mm
with W as grinding work in kJ/kg, c as grinding coefficient, dA as grain size of the source material and dE as grain size of the ground material.
A reliable value for the grain sizes dA and dE is d80. This value signifies that 80% (mass) of the solid matter has a smaller grain size. The Bond's grinding coefficient for different materials can be found in various literature. To calculate the KICK's and Rittinger's coefficients following formulas can be used
with the limits of Bond's range: upper dBU = 50 mm and lower dBL = 0.05 mm.
To evaluate the grinding results the grain size disposition of the source material (1) and of the ground material (2) is needed. Grinding degree is the ratio of the sizes from the grain disposition. There are several definitions for this characteristic value:
- Grinding degree referring to grain size d80
- Instead of the value of d80 also d50 or other grain diameter can be used.
- Grinding degree referring to specific surface
- The specific surface area referring to volume Sv and the specific surface area referring to mass Sm can be found out through experiments.
- Pretended grinding degree
- The discharge die gap a of the grinding machine is used for the ground solid matter in this formula.
Grinding machines
In materials processing a grinder is a machine for producing fine particle size reduction through attrition and compressive forces at the grain size level. See also crusher for mechanisms producing larger particles. In general, grinding processes require a relatively large amount of energy; for this reason, an experimental method to measure the energy used locally during milling with different machines was recently proposed.[3]
Ball mill
A typical type of fine grinder is the ball mill. A slightly inclined or horizontal rotating cylinder is partially filled with balls, usually stone or metal, which grind material to the necessary fineness by friction and impact with the tumbling balls. Ball mills normally operate with an approximate ball charge of 30%. Ball mills are characterized by their smaller (comparatively) diameter and longer length, and often have a length 1.5 to 2.5 times the diameter. The feed is at one end of the cylinder and the discharge is at the other. Ball mills are commonly used in the manufacture of Portland cement and finer grinding stages of mineral processing, one example being the Sepro tyre drive Grinding Mill. Industrial ball mills can be as large as 8.5 m (28 ft) in diameter with a 22 MW motor,[4]drawing approximately 0.0011% of the total world's power (see List of countries by electricity consumption). However, small versions of ball mills can be found in laboratories where they are used for grinding sample material for quality assurance.
The power predictions for ball mills typically use the following form of the Bond equation:[2]
where
- E is the energy (kilowatt-hours per metric or short ton)
- W is the work index measured in a laboratory ball mill (kilowatt-hours per metric or short ton)
- P80 is the mill circuit product size in micrometers
- F80 is the mill circuit feed size in micrometers.
Rod mill
A rotating drum causes friction and attrition between steel rods and ore particles.[citation needed] But note that the term 'rod mill' is also used as a synonym for a slitting mill, which makes rods of iron or other metal. Rod mills are less common than ball mills for grinding minerals.
The rods used in the mill, usually a high-carbon steel, can vary in both the length and the diameter. However, the smaller the rods, the larger is the total surface area and hence, the greater the grinding efficiency[5]
Autogenous mill
Autogenous or autogenic mills are so-called due to the self-grinding of the ore: a rotating drum throws larger rocks of ore in a cascading motion which causes impact breakage of larger rocks and compressive grinding of finer particles. It is similar in operation to a SAG mill as described below but does not use steel balls in the mill. Also known as ROM or "Run Of Mine" grinding.
SAG mill
SAG is an acronym for Semi-Autogenous Grinding. SAG mills are autogenous mills but use grinding balls like a ball mill. A SAG mill is usually a primary or first stage grinder. SAG mills use a ball charge of 8 to 21%.[6][7] The largest SAG mill is 42' (12.8m) in diameter, powered by a 28 MW (38,000 HP) motor.[8] A SAG mill with a 44' (13.4m) diameter and a power of 35 MW (47,000 HP) has been designed.[9]
Attrition between grinding balls and ore particles causes grinding of finer particles. SAG mills are characterized by their large diameter and short length as compared to ball mills. The inside of the mill is lined with lifting plates to lift the material inside the mill, where it then falls off the plates onto the rest of the ore charge. SAG mills are primarily used at gold, copper and platinum mines with applications also in the lead, zinc, silver, alumina and nickel industries.
Pebble mill
A rotating drum causes friction and attrition between rock pebbles and ore particles. May be used where product contamination by iron from steel balls must be avoided. Quartz or silica is commonly used because it is inexpensive to obtain.
High pressure grinding rolls
A high pressure grinding roll, often referred to as HPGRs or roller press, consists out of two rollers with the same dimensions, which are rotating against each other with the same circumferential speed. The special feeding of bulk material through a hopper leads to a material bed between the two rollers. The bearing units of one roller can move linearly and are pressed against the material bed by springs or hydraulic cylinders. The pressures in the material bed are greater than 50 MPa (7,000 PSI). In general they achieve 100 to 300 MPa. By this the material bed is compacted to a solid volume portion of more than 80%.
The roller press has a certain similarity to roller crushers and roller presses for the compacting of powders, but purpose, construction and operation mode are different.
Extreme pressure causes the particles inside of the compacted material bed to fracture into finer particles and also causes microfracturing at the grain size level. Compared to ball mills HPGRs achieve a 30 to 50% lower specific energy consumption, although they are not as common as ball mills since they are a newer technology.
A similar type of intermediate crusher is the edge runner, which consists of a circular pan with two or more heavy wheels known as mullers rotating within it; material to be crushed is shoved underneath the wheels using attached plow blades.
Buhrstone mill
Another type of fine grinder commonly used is the buhrstone mill, which is similar to old-fashioned flour mills.
Vertical shaft impactor mill (VSI mill)
A VSI mill throws rock or ore particles against a wear plate by slinging them from a spinning center that rotates on a vertical shaft. This type of mill uses the same principle as VSI Crusher
Tower mill
Tower mills, often called vertical mills, stirred mills or regrind mills, are a more efficient means of grinding material at smaller particle sizes, and can be used after ball mills in a grinding process. Like ball mills, grinding (steel) balls or pebbles are often added to stirred mills to help grind ore, however these mills contain a large screw mounted vertically to lift and grind material. In tower mills, there is no cascading action as in standard grinding mills. Stirred mills are also common for mixing quicklime (CaO) into a lime slurry. There are several advantages to the tower mill: low noise, efficient energy usage, and low operating costs.
Types of grinding mills
- windmill, wind powered
- watermill, water powered
- horse mill, animal powered
- treadwheel, human powered (archaic: "treadmill")
- ship mill, floats near a river bank or bridge
- arrastra, simple mill for grinding and pulverizing (typically) gold or silver ore.
- roller mill, an equipment for the grinding or pulverizing of grain and other raw materials using cylinders
- Stamp mill, a specialized machine for reducing ore to powder for further processing or for fracturing other materials
- a place of business for making articles of manufacture. The term mill was once in common use for a factory because many factories in the early stages of the Industrial Revolution were powered by a watermill, but nowadays it is only used in a few specific contexts; e.g.,
- bark mill produces tanbark for tanneries
- cider mill crushes apples to give cider
- gristmill grinds grain into flour
- oil mill, see expeller pressing, extrusion
- paper mill produces paper
- sawmill cuts timber
- starch mill
- steel mill manufactures steel
- sugar mill (also called a sugar refinery) processes sugar beets or sugar cane into various finished products
- textile mill (disambiguation)
- silk mill, for silk
- flax mill, for flax
- cotton mill, for cotton
- huller (also called a rice mill, or rice husker) is used to hull rice
- powder mill produces gunpowder
- Ball mill
- Bead mill
- Coffee mill
- Colloid mill
- Conical mill
- Disintegrator
- Disk mill
- Edge mill
- Gristmill, also called flour mill or corn mill
- Hammermill
- IsaMill
- Jet mill
- Mortar and pestle
- Pellet mill
- Planetary mill
- Stirred mill
- Three roll mill
- Vibratory mill
- VSI mill
- Wiley mill
- Windmill
If you don't have the money to buy your own pellet maker then we suggest you buy a grinder and learn how to add your own homemade glue to and run it through a plastic mill of your own making.
Homemade glue recipes
1. Flour glue recipe
The most basic of the homemade glue recipes, which you may already be familiar with, is just made of flour and water. It tends to dry out over time and stop holding together whatever it was holding together, but it’s fine for, say, making decorations a few hours before a party.
- Blend flour with water until it’s near the consistency of pancake batter.
- Beat your mixture until it’s smooth.
- Pour it into a saucepan on medium heat.
- Constantly stir while bringing it slowly to a boil.
- Let it cool before using.
Store it in a sealed container and apply it with a brush. If it dries out, you can mix a little warm water into it.
2. Cornstarch glue recipe
This is another basic glue recipe that works better than the flour recipe. It’s good for holding paper together without making ripples or bubbles.
- Pour 3/4 cup of water in a saucepan over medium heat.
- Add 1/4 cup cornstarch, 2 tablespoons light corn syrup and 1 teaspoon white vinegar.
- Whisk the ingredients together until they’re blended well.
- Stir the mixture constantly until it thickens.
- In the airtight container where you want to store your glue, whisk 1/4 cup cornstarch and 1/4 cup water together until smooth.
- Take the saucepan off heat. Slowly add the mixture from your saucepan into the container, and keep whisking constantly so everything blends together smoothly.
- Let it cool to room temperature before using.
3. Corn syrup glue recipe
This makes yet another basic homemade glue. NOTE: I keep getting questions about whether any of these work for slime. I haven’t tested it myself, but several readers report that this recipe works great for slime.
- In a small saucepan, mix 3/4 cup water with 2 tablespoons corn syrup and 1 tablespoon white vinegar.
- Bring the mixture to a rolling boil.
- In bowl, mix 2 tablespoons cornstarch with 3/4 cups cold water.
- Slowly add the cold mixture into the hot mixture. Stir constantly for one minute.
- Remove from heat.
- Once it’s cooled, pour the mixture into its final container. Let it stand overnight at room temperature before using.
4. Basic paste recipe
This recipe makes a simple paste suitable for kids’ crafts.
- Slowly add cold water to 1/2 cup flour until the consistency is like heavy cream.
- Simmer in a saucepan for 5 minutes, stirring constantly.
- Let it cool before use.
5. No-cook paste
This recipe is so easy, and kids can totally make it themselves. It makes a thick paste that won’t hold forever, but is suitable for kids’ crafts.
- Mix 1/2 cup flour water in a bowl, adding the water slowly while stirring, until the consistency is gooey.
- Stir in a pinch of salt.
6. Waterproof glue (without milk)
When you’re gluing something together that’s going to go under water, you need a glue that doesn’t melt. This is that recipe. This homemade glue needs to be applied warm – the first time you cook it up, that’s simple. For future applications, put your container in a bowl, pan or sink of hot water to warm it up again. Apply it with a brush. It can take a few days to gel, but it’s good for lots of crafts.
A lot of waterproof homemade glue recipes include milk, which of course spoils quickly. This one will actually keep for a while, but isn’t quite strong enough to hold together something like a broken china plate.
- Boil 6 tablespoons of water in a saucepan.
- Take the saucepan off heat. Stir in 1/2 ounce (14 grams) of gelatin – that’s 2 packets in most brands I know of in the US. (Unless you want your glue to smell like a gelatin flavor, which is an interesting thought.)
- Once the gelatin has dissolved, add 2 tablespoons of white vinegar and a teaspoon of glycerine.
- Stir well. Let it cool a little before pouring it into your airtight container.
7. Waterproof glass glue (with milk)
This homemade glue can be used to mend broken china, like super glue. It also works well to glue labels on cans and jars, or to glue glass to other surfaces. All in all, it’s pretty strong. For gluing glass to other surfaces, use it while it’s liquid (warm it by putting the container in a pan of hot water). To glue pieces of glass together, use it in its gelled (room temperature) state.
Note from reader Eva Stosic, “The milk glue will last forever if you add mint extract. I make clay and it lasts no mildew or mold.”
- Pour two tablespoons of cold water into a small bowl.
- Sprinkle 2 packets of unflavored gelatin over the water and set aside for about an hour.
- Heat 3 tablespoons of skim milk to just below boiling and pour it into the gelatin and water.
- Stir the mixture until the gelatin is completely dissolved.
- Optionally, add a few drops of clove oil as a preservative if you’re not going to use all the glue immediately. (With clove oil, the glue will keep for a day or so – when it starts smelling like spoiled milk, throw it out.)
- Or instead of clove oil, add a few drops of mint extract, which one reader says will make it last forever. Try it and let me know in the comments!
8. Papier-Mache paste
This paste will keep for several weeks. It’s perfect for gluing down layers of papier-mache or collages.
- Mix 1/4 cup of flour into a cup of room temperature water until the consistency is runny.
- In a large saucepan, heat 5 cups of water to a gentle boil. Stir your flour and water mixture into it.
- Gently boil for 2 or 3 minutes, stirring constantly.
- Let it cool before use.
9. Gum Arabic (Superglue) recipe
This glue is designed to mend broken china and crockery. For that specific use, it should perform a little better than the glass glue at #7. Use a matchstick to apply a very thin coat of it to both sides of broken crockery, and then fit the pieces together. As you would do with Superglue, hold the pieces firmly together until the glue dries, which could be up to an hour. Let it dry at least twenty-four hours before you use or wash the mended piece. This glue will keep for a year.
- Mix 3 tablespoons of gum arabic, 1 tablespoon of glycerine and 1/2 teaspoon of water thoroughly in a bowl.
- Put the mixture in an airtight container. Will keep about 1 year. To Use: Apply a thin coat of the glue to each surface and fit the pieces together. Hold firmly until the glue dries – this could take an hour or so. Let the piece dry thoroughly (24 hours) before washing or using.
10. Envelope/stamp glue
If you making your own envelopes, you’ll need lickable glue for them.
- 3 tablespoons white vinegar
- 1 envelope unflavored gelatin
- 1 teaspoon sugar
- Optional: 1 teaspoon vanilla extract or mint extract
Put the vinegar in a small saucepan and bring to a boil. Add in the gelatin and stir to completely dissolve it. Add the sugar and extract and stir some more. Use a brush to apply it to homemade envelopes or stamps, and let it dry for several hours. Store the unused glue in the refrigerator to keep it from molding. It keeps for a week or two.
11. Library paste
This paste is used for binding paper and paperboard.
Mix all the ingredients except the clove oil together in a saucepan. Cook on medium heat until the mixture is clear and thick. Optionally add your 30 drops of clove oil as a preservative. Store in small jars, so that only a small amount is being exposed to air and dried out every time you open it.
Note: if you’re looking for wallpaper paste, I haven’t tested it myself. But both the Corn Starch Glue (#2) and the Library Paste (#11) are recommended
No comments:
Post a Comment